New Thermoset Composite FLAMEVEX™ Is Key Material In EV Battery Packs That Pass Rigorous China Bonfire Testing
High-performance material addresses flame resistance, strength and light weighting challenges
IDI Composites International is introducing a new thermoset composite material delivering critical performance benefits for the "new energy vehicles" market. Deployed in electric vehicle (EV) new energy vehicles (NEV) applications, FLAMEVEX™ is a flame-resistant lightweight composite. FLAMEVEX™ has been used on battery packs, which have passed the stringent Chinese Standard GB/T 31467.3 test, commonly known as the China bonfire test. FLAMEVEX™, offers designers a strong, lightweight and cost-effective alternative to steel and aluminum materials traditionally used to enclose battery packs in EVs and NEVs
EV and NEV designers have long faced the dilemma of balancing flame resistance, strength and light weighting requirements as they develop solutions for critical applications like the vehicle battery enclosure. Battery packs take up significant space in vehicle designs and must offer dimensional strength as well as resistance to flame and high temperatures. Strong and durable, steel has long been a preferred material, but the heavy weight burden makes it a poor choice. While aluminum and carbon fiber provide designers lightweight options, these technologies are still in development stages making them inherently risky and very costly. FLAMEVEX™ brings to market a thermoset composite technology that is both easy to use and proven in research studies and "on-the road" actual applications.
"Thermoset composites represent an ideal replacement for metals in these kinds of battery enclosures," noted Yves Longueville, General Manager for IDI Composite Materials (Shanghai) - China. "Thermoset materials can be formed into complex shapes and they are also strong and lightweight. Beyond these benefits, a high level of fire performance distinguishes FLAMEVEX™ from traditional SMC composites," Longueville explained. "FLAMEVEX™ maintains its impressive fire performance even at low thicknesses, and without compromising the strength or moldability of the compound. It is the best choice for designers developing high performing and affordable products."
Working in collaboration with OEMs and Tier 1 partners, IDI FLAMEVEX™ materials have been used on battery packs which have passed the Chinese bonfire test—the world's most stringent fire resistance standard—at thicknesses as low as 2.5 mm. Battery packs made with FLAMEVEX™also meet the UL 5VA standard. Recognizing that industry standards are continuing to evolve, FLAMEVEX™ materials can be manufactured to fit specific flame resistance standards for OEMs and Tier 1 manufacturers.
The market for EV and NEV vehicles is growing exponentially, with sales expected to double in 2020, reaching four million new cars globally. "As cost of ownership goes down, range increases and emissions requirements become tighter, electric and alternative fuel vehicles are only becoming more attractive to buyers," explained IDI Vice President and Group Director of EV Market Development Ramon Rodriguez-Irizarry. "With FLAMEVEX™, we're not only helping to meet a need for OEMs and designers, we're introducing a material that contributes to the strength, safety and affordability of this next generation of vehicles for consumers around the world."
In this rapidly changing and growing industry, manufacturers are seeking materials partners with both expertise and the capability to innovate. "Our vast experience in moldable compounds puts IDI in a unique position to keep pace with the changing landscape of requirements for EV and NEV parts," said Rodriguez-Irizarry. "IDI Composites has worked closely with OEMs and Tier 1 suppliers to meet their flame performance targets and optimize materials to fit the special shapes their newest designs call for. With these composites now in mass production, we look forward to introducing FLAMEVEX™ SMC to even more manufacturers to help them fulfill their goals for strength, design and safety in not only battery pack covers, but all areas of EV and NEV design."
About IDI Composites International
IDI Composites International (IDI) is the premier global custom formulator and manufacturer of thermoset molding compounds for channel partners and OEMs. The company provides customized sheet molding compounds (SMC), polyester/vinyl ester-based bulk molding compounds (BMC), new line of Structural Thermoset Composites (STC®) that are manufactured in both sheet and bulk formats for the most demanding applications in markets such as Military & Aerospace, Transportation, Safety, Medical, Electrical, Oil & Gas, Alternative Energy and Marine. Additional information can be found here.
Headquartered in a 120,000 square foot manufacturing facility and research center in Noblesville, IN (USA), IDI has a strong presence in the international thermoset composites market with wholly owned manufacturing facilities for these materials in France, China and México. With more than 50 years of leadership experience, IDI works closely with customers to identify the optimal thermoset molding compound for each application. The company has substantial R&D resources, plus excellent chemical engineering, ISO-certified manufacturing, and comprehensive quality control.
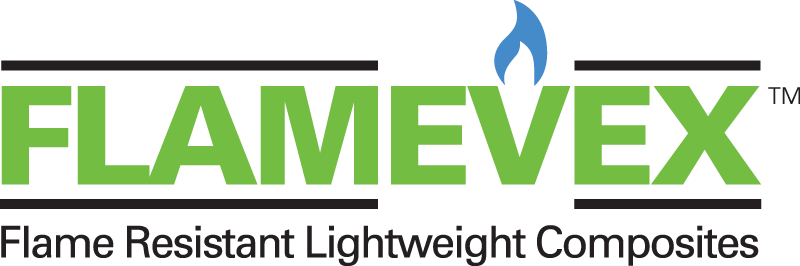
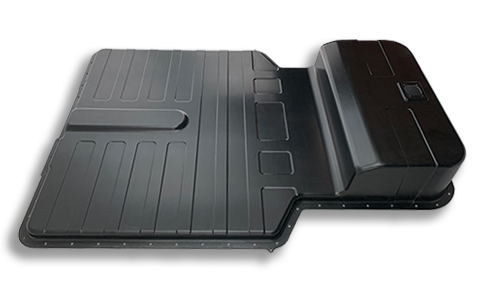